Meet Julie
“Since Scan for Safety has been implemented, it has released – on average – an hour and a half of time back for me, every day.”
Julie McDonald is a Stock Controller in NHS Lothian’s Interventional Radiology Department. As the first board and department in NHSScotland to implement Scan for Safety’s Point of Care, Julie was at the forefront of the efforts and
planning in preparation for the commencement of launch.
Here she shares the benefits of the programme for her role, and the realities associated with getting ‘Scan for Safety’ ready.
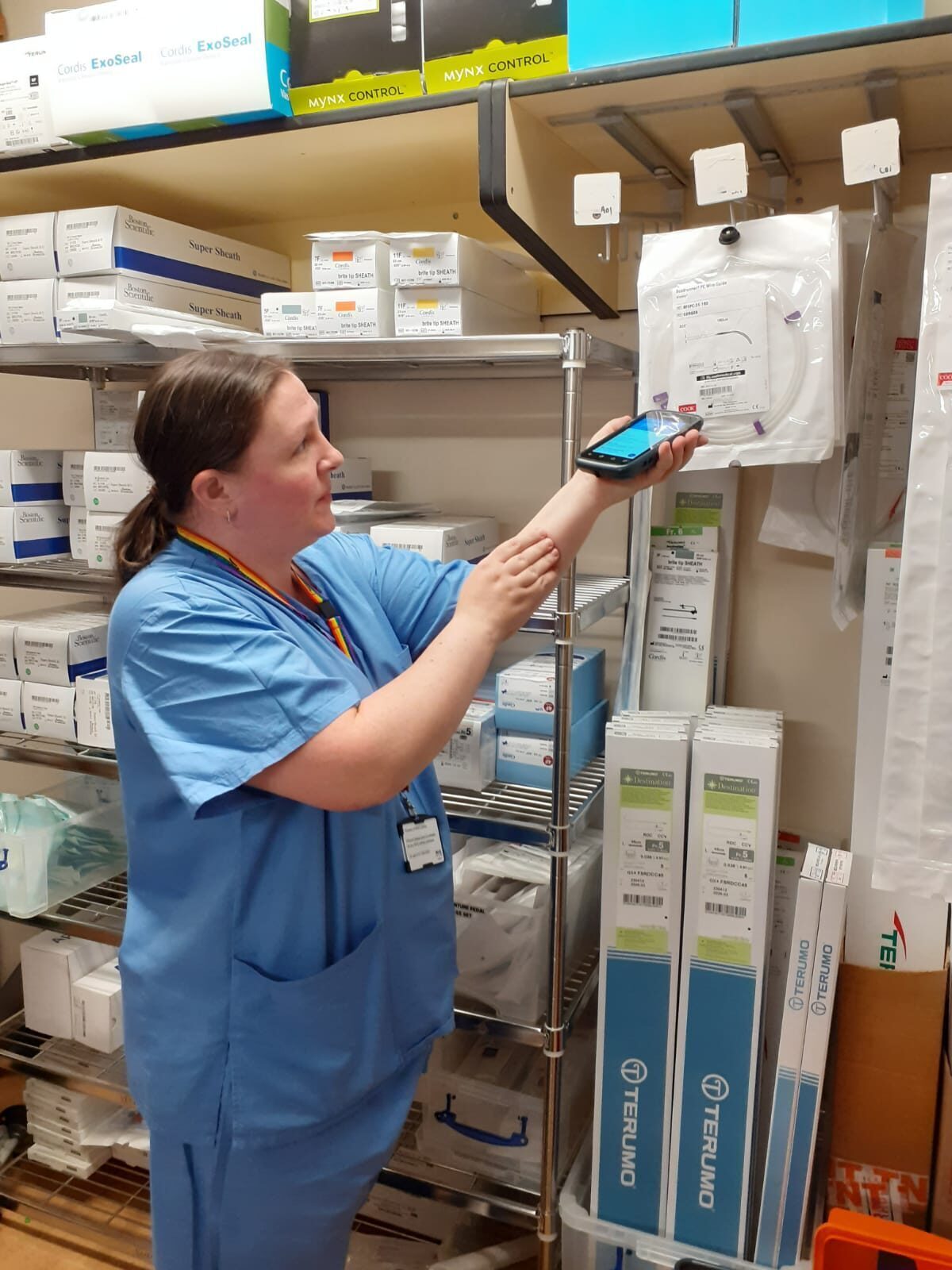
“The data you can extract from Scan for Safety is unbelievable. Seeing what all the different bits and functions do. Looking at real time live data around what products are being used when. The system we have now with Point of Care and Inventory Management is 100% better than what we had. It’s transformed my job.
“However, getting to this point was a big task and the commitment of time and effort needed cannot be underestimated. The importance of getting the stock information right, is absolutely key. Data that Scan for Safety offers you will only ever be as good as the information you put in. So to get to a good place, required a major commitment of time and interrogation.
“Every single one of the 1200+ items we deal with had to be checked and inputted individually – from code checks to LOT numbers. Our previous system was notoriously glitchy and this meant that time was being eaten into every day just to find work arounds and amend any errors it was causing. So when it came to getting information ready for Scan for Safety, there was extra rigour in having to double and triple check things because of doubts in the quality of stock info we had on the other system.
“In addition, getting ready for implementation required a commitment to understanding how everything worked. How the data and information was used by all and how things were receipted at different parts of the hospital journey. I’ve since built up really good working relationships across our board from the procurement team to the warehouse teams, and we all have a far better understanding of each other’s roles and how things work.
“In truth, my job was 100 times harder before, than it is now. Since Scan for Safety has been implemented, it has released – on average – an hour and a half of time back for me, every day. I get to manage my time far more effectively and for our department, I can now far better manage the overall stock control including getting the time needed for mini stock takes. This means my stock is always accurate. From a financial standpoint, we now always know exactly where we stand.
“As a department, we’re also not having to order as much stock. Previously there would be boxes and boxes of stuff on the shelves and it wasn’t always easy to be aware of what was needed or being ordered. That’s now changed.
“For staff it’s been a bit of culture change too. They were used to seeing the shelves packed with stuff. They have had to since grow trust that we don’t need to have so much in stock. That we have enough and always will because of how we are now tracking things. The system alerts me when we need to re-order. I have everything set up for re-orders so that when we reach certain levels, it can trigger the alert to order. This is helping us reduce the risks of wastage.
“Overall, it really takes the whole department to get on board with this – everyone has a role to get to grips with what this can do for all of us.
“There shouldn’t be underestimations of the time to get Scan for Safety ready, especially for departments who may not have someone in a role like mine. Not every department will have a stock controller. But there are a lot of wins with this system and the benefits it will bring also should not be underestimated.”